The DPF Cleaning Methods Explained:
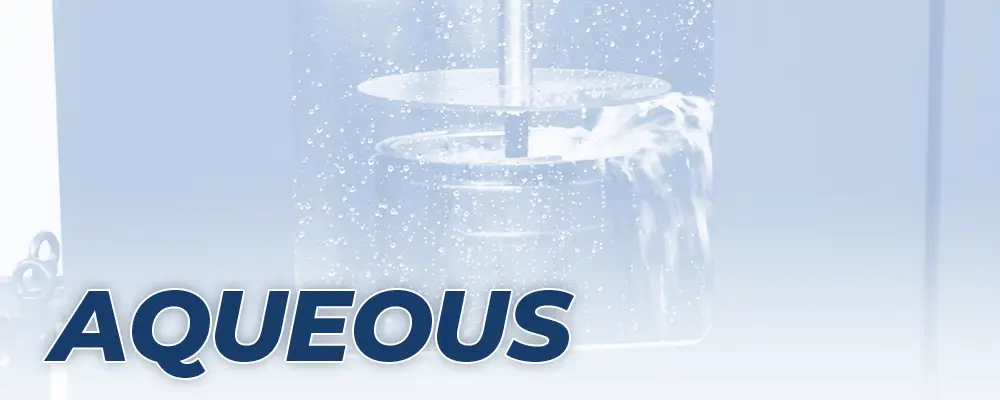
Aqueous DPF Cleaning:
Aqueous DPF cleaning continues to rise in popularity due to its ultra-fast turnaround and versatility in safely cleaning filters of various sizes and shapes without damaging their substrate. The water-based, non-destructive cleaning process, allows effective cleaning within a few hours, getting your trucks back on the road the same day. Also, it eliminates the need to cut open & reassemble filters with odd-shaped inlets and/or outlets, as it washes and dries all manner of filters with ease.
This process is multi-stage. Benchmarking and inspections pre and post-cleaning are important to measure the effectiveness. The Filtertherm Aqueous machine, for example, utilizes a pre-soak surfactant stage to loosen ash particles, then the removal of soot and ash from the DPF substrate using a computer-controlled, low-pressure, high-volume, flow of water. The wastewater is filtered and recirculated to save on water use.
Risky pressure washing is not needed here. The process is eco-friendly, mild on the filter due to lower temperatures, and suitable for larger-scale cleaning operations. Aqueous DPF cleaning remains a practical and convenient option for maintaining diesel filters quickly and effectively.
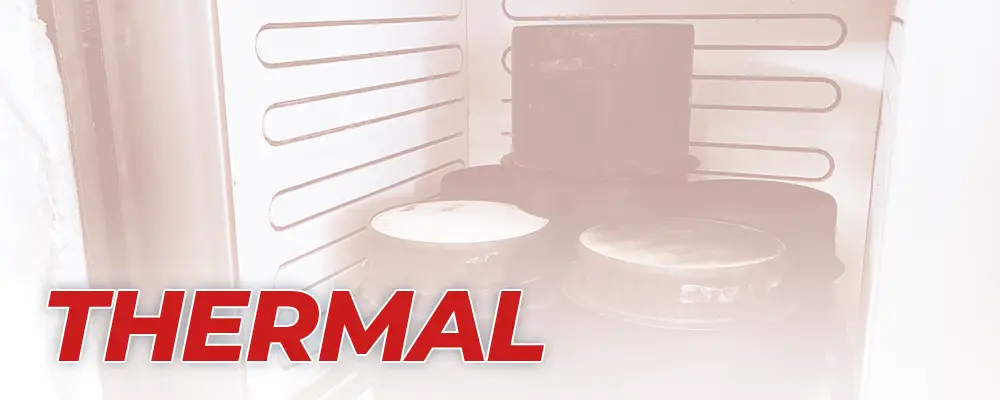
Thermal DPF Cleaning:
Thermal DPF cleaning is a time-tested process ideal for standard-shaped filters, the process typically takes about 24 hrs or less and does not require huge amounts of water or chemical treatments. This method utilizes high temperatures with precise heating/cooling cycles, to burn away accumulated PM (particulate matter) and other contaminants. The baking cycle, often done overnight, is followed by a cooling period (we have ways to speed up cooling times). Few ovens are high-capacity, allowing for successfully cleaning several filters simultaneously, making them ideal for high-volume fleet operations. One such DPF Cleaning oven is this one by Filtertherm that has enough internal space to clean a whole One-Box. Additionally, thermal cleaning can burn off various contaminants that can “soak” a filter due to upstream issues/leaks.
The Thermal process we use begins with a complete inspection/benchmarking and then a blowout to remove any loose materials still in the filter. Then a precise bake overnight in the thermal oven to oxidize the soot, followed by a cool-down phase and then pulse cleaning/air to blow out the remaining ash. Finally, a post-clean inspection and benchmarking are performed to determine the effectiveness of the cleaning. In some cases, a filter may require a second baking if it hasn’t been serviced in a while.
A well-designed DPF Cleaning oven allows the technician to choose the filter material type, (which includes silicon carbide, cordierite, metal mesh, or other materials, each has an ideal temp and cycle). Using the right heating/cooling cycle settings helps make sure filters are not damaged during the thermal cleaning process.
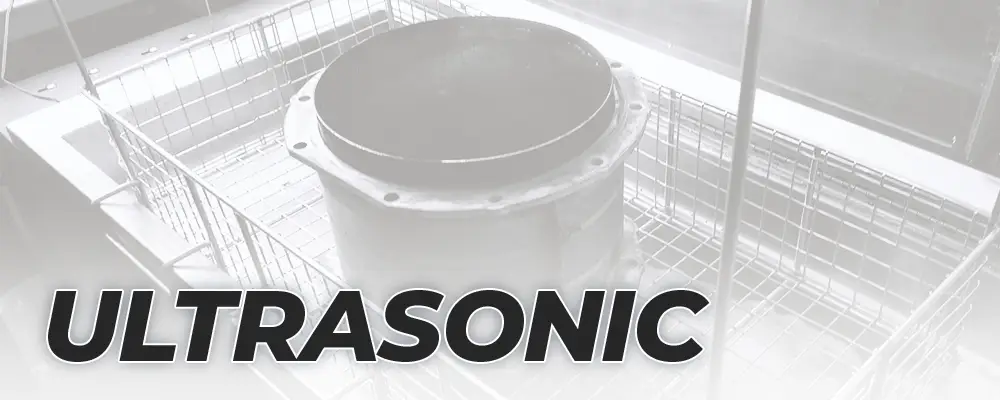
Ultrasonic DPF Cleaning:
Ultrasonic DPF cleaning has recently been getting some interest in the industry. This method involves completely submerging the filter in a large vat and utilizing high-frequency sound waves to remove the particulate matter. These sound waves create small bubbles, generated by specialized equipment with cleaning solution, removing the ash. While generally gentle and suitable for various filter types, it’s crucial to ensure the cleaning solution is compatible with the filter being cleaned. For example: some retrofit DPF filters contain material (matting) in their construction that should not get wet.
To purchase a quality setup, the ultrasonic process often has a steep upfront cost (Note: buyers beware – there are cheap versions on the market with fewer nodes that result in substandard results).
There are ways ultrasonic can be automated for large-scale operations. This often involves quite a bit of expert set-up, calibration, and upkeep.
While it’s excellent at cleaning most ash, it might not be as effective for certain types of contaminants, often causing the DPF to be cleaned again or baked in an oven. Since the cleaning solution and debris need to be flushed out and the filter completely dried before reinstalling, this can cause even longer turnaround times (as much as an extra day) in getting the truck back on the road.
DPF Cleaning Methods Quick Guide:
Aqueous DPF Cleaning: Growing in popularity and adoption for its cost-effectiveness and versatility in handling various filter types quickly. Ideal for operations that need ultra-fast turnaround times and control.
Thermal DPF Cleaning: A time-tested approach known for its simplicity and effectiveness in removing soot & contaminants. Ideal for fleet operations that need to clean a lot of filters at once and need predictable outcomes.
Ultrasonic DPF Cleaning: Has been getting more attention. It is a versatile and effective option that employs using sound waves & solvents to dislodge particles from filters and other types of parts. The additional rinsing/drying time, complexity & cost of operation of this developing tech might discourage some users.
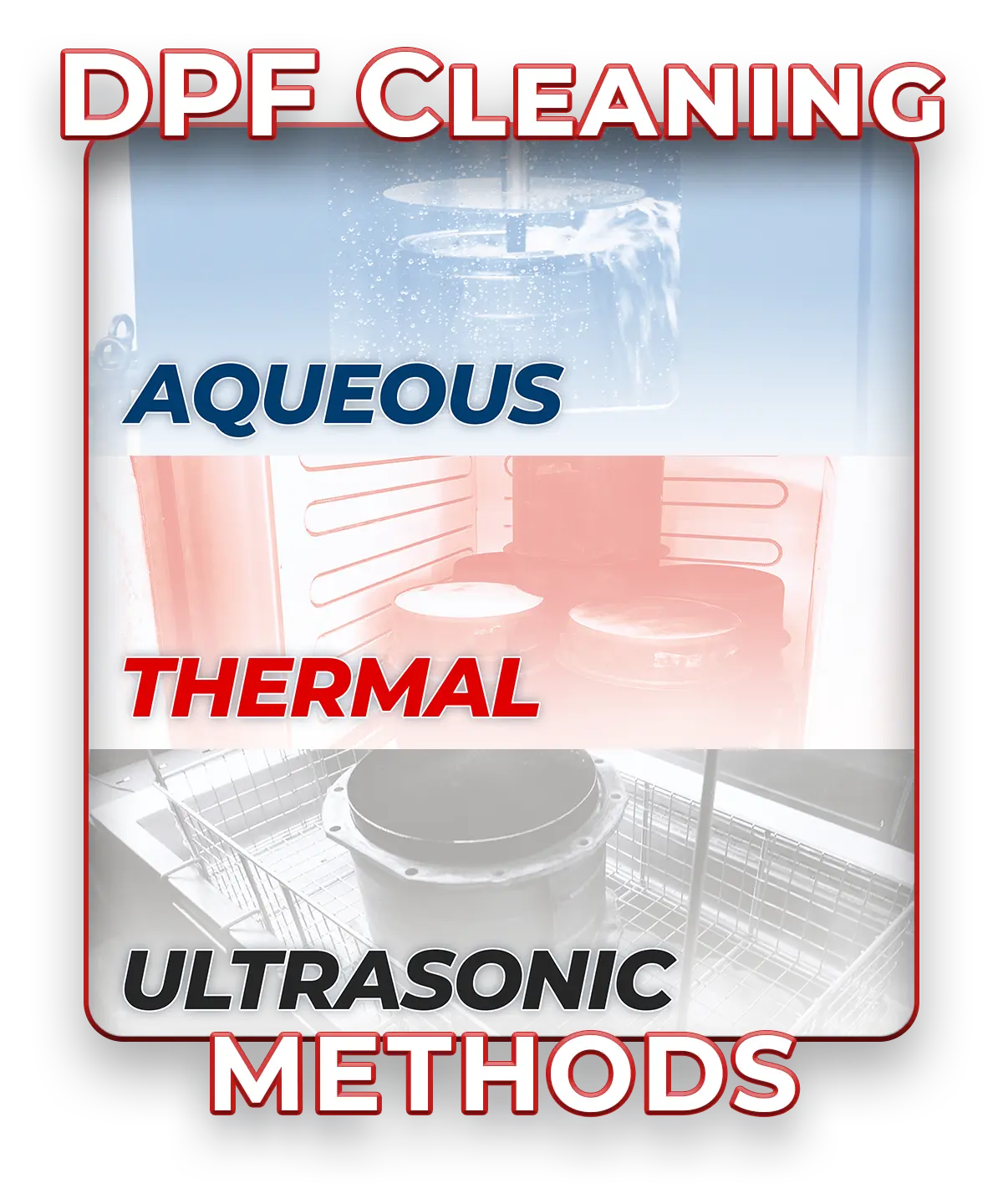
Get the right DPF Cleaning solution for your FLEET.
Give us a call. Get Answers.
Use our ROI tool to see how quickly this investment can save your fleet time and money. Financing is now available. Check it out!
Call or email to schedule a meeting with our National Sales Manager, Anthony Soto.